Accreditation of Equipment and Production Facilities
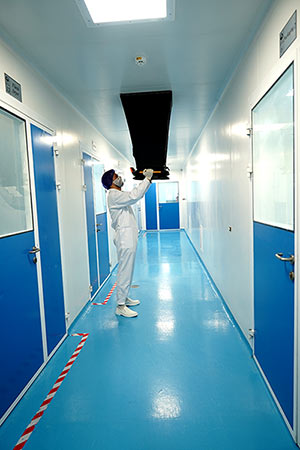
A clean room is a modular environment meticulously controlled for several critical factors including temperature, airborne particles, microbial load, relative humidity, pressure differentials, barometric pressure, and airflow.
The validation of a clean room is performed for several essential reasons, primarily:
- Ensuring the design of cleanroom components is suitable for its intended use.
- Confirming that facilities, equipment, and environment meet the User Requirements Specifications (URS).
- Verifying that the facilities, equipment, and environment adhere to the legal regulations specific to the country of operation.
- Ensuring that the collective system of facilities, equipment, and environment meets designated standards.
Clean rooms undergo an initial validation, followed by the issuance of a certification in accordance with the class defined by ISO 14644 standards. Each clean room class has distinct requirements, and appropriate special facilities must be constructed to align with its specific classification.
Cleanroom Accreditation Lifecycle
The validation of a cleanroom follows a well-defined lifecycle, structured into five distinct phases. Each phase carries out specific tasks aimed at managing changes within the modular environment. The overall process of cleanroom validation is divided into these five key stages. It begins with the design control phase and concludes with the monitoring and control phase. Any alterations to equipment or control parameters post-validation necessitate the re-validation of the cleanroom.
Qualification:
Qualification is the first step and one of the most important factors in creating and evaluating a comprehensive quality management system. Due to the fact that the processes are carried out by equipment and machines, first of all, quality assurance or their qualification is prioritized.
In a new Altasys pharmaceutical company, it is necessary to first mention all accreditation and quality assurance matters in a document called the Comprehensive VMP Accreditation Program, which is mainly divided into two categories: quality assurance and accreditation.
Checking the quality of devices and systems:
- Checking the quality of air conditioning systems and clean rooms
- Verification of the quality of support facilities
- Quality verification and validation of water systems (pure water and water for injection)
- Checking the quality of devices
Once the quality assurance phase is complete, validation activities are performed as outlined below:
Validations:
- Validation of the production process
- Validation of aseptic processes, if applicable
- Validation of cleaning procedures
- Validation of analytical methods
- Accreditation of computer systems
This structured approach ensures that Altasys upholds the highest standards in quality management, laying a solid foundation for exceptional performance and compliance.
In the First Phase: Design Qualification (DQ)
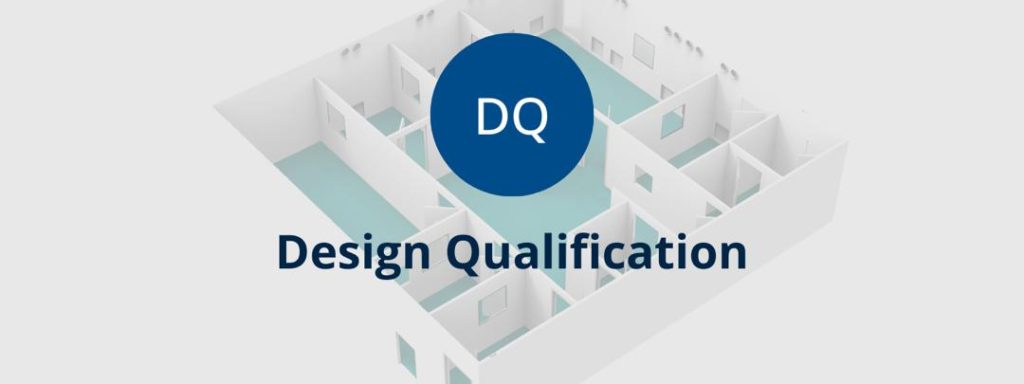
cleanroom validation commences with ensuring the quality of the design. The aim of this stage is to provide objective evidence that the design meets its intended purpose. Design qualification involves verifying that the specified requirements, as outlined in the acceptance criteria, are fulfilled. These criteria, explicitly or implicitly set by the employer at the project’s outset, must be clearly defined in the DQ protocol. Therefore, the DQ protocol should address the following:
- User Required Specifications (URS)
- Seller documentation and details
- Equipment layout
- Purchase orders for various equipment
- Design documentation
- Factory Acceptance Tests (FAT)
- As-built plans
- Data sheets
The output of the design quality assurance phase is a report generated according to a Standard Document List (SDL) file, which documents the following:
- Design requirements
- Tender requirements
- Purchase and order documentation
- List of documents provided by the seller
- Construction plans
- List of components, equipment, and parts used
- Checklists
- Factory acceptance tests
Once the quality of the design is verified, the next step is to proceed with the installation phase for equipment, air conditioners, and other necessary setups. Completing the Design Qualification (DQ) phase is a prerequisite for beginning the Installation Qualification (IQ) phase.
Second phase: Installation Qualification
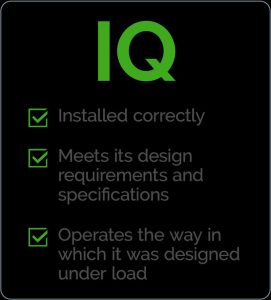
The purpose of this stage is to ensure the quality of the installation of equipment such as air conditioners, panels, doors, and more. We refer to this stage as IQ (Installation Qualification). During the clean room equipment installation phase, we operate through verification, meaning the installed equipment must comply with both user and design requirements. The IQ phase focuses on the following aspects, which should be detailed in the IQ protocol:
- HVAC calibration
- P&ID loop verification
- Review of HEPA filter integrity test data
- Calibration status of critical equipment
- Clean room installation site acceptance tests (SAT)
- Equipment installation quality assurance tests
- Piping and welding documentation
- Verification of tools
- Standard operating procedures and work instructions for the system
The output of this stage should be a comprehensive IQ report that addresses all of the above elements. Additionally, a detailed file should be maintained documenting the following:
- Project modifications
- IQ test performance
- Calibration records
- Documents supplied by vendors
- Equipment certificates
- Deviations noted during installation
- Clean room site acceptance tests (SAT)
- List of consumables, installed equipment, material flow chambers, etc.
- List of spare parts
- Environmental survey report
- List of implementation methods and instructions
Installation quality assurance (IQ) is a prerequisite for initiating the operational quality assurance (OQ) phase.
The third phase: Verification of Operational Quality (OPERATION QUALIFICATION)
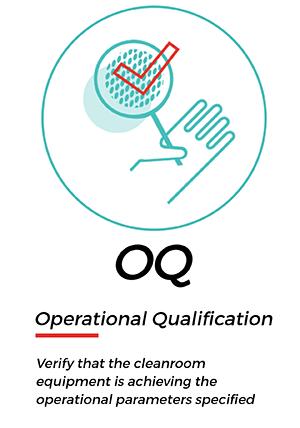
The purpose of this phase is to confirm the operational quality (OQ) of the cleanroom. This phase provides objective evidence that the cleanroom meets design specifications and user requirements while operating within specified and acceptable limits.
In the OQ protocol, the following aspects should be considered:
- Performance testing of the HVAC (Heating, Ventilation, and Air Conditioning) system based on specified requirements for critical alarms, ensuring the cleanroom monitoring system generates alarms during emergencies.
- Verification of interlock alarms.
- Validation of critical operating parameters as outlined in the cleanroom data sheet.
- Integrity testing of filters.
- Adherence to standard cleanroom performance criteria
- Measurement of airspeed and airflow.Airflow patterns
- pressure difference
The OQ phase should also consider the “Worst Case” scenario. For “Worst Case” design in cleanroom performance, critical operating parameters are identified based on cleanroom data information. The operating range as well as the critical range for each parameter should be carefully designed and documented. These should encompass the following items:
- Maximum and minimum temperature
- Maximum and minimum humidity
- Maintenance schedule
- Personnel contamination
“Worst Case” assessments are typically conducted at both maximum and minimum parameter values.
The outcome of this phase is a documented report, referred to as an OQ, which addresses alarms and user-defined cleanroom performance requirements.
The fourth phase: Performance Validation
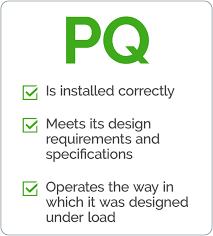
The goal of Cleanroom Performance Qualification (PQ) certification is to provide objective evidence that the cleanroom reliably operates within specified parameters to achieve a desired environmental outcome. Cleanroom performance qualification involves testing and monitoring the following aspects:
- Airborne particle levels
- Surface particle counts
- Microbial load
- Relative humidity
- Pressure differentials
- Temperature
The outcome of the PQ phase is a comprehensive, documented report that evaluates cleanroom performance based on equipment parameters. PQ is a crucial step required for certification.
CLEANROOM Certificate
Certified cleanrooms are categorized by “cleanliness classes” or “cleanroom classes”. These certifications are based on adherence to specific cleanliness standards, tailored according to the customer’s requirements. The cleanroom classes are specified in ISO 14644. To achieve a “room cleanliness class” certification, at least the following ten tests must be successfully passed:
- Airborne particle counting test
- Air flow test
- Air pressure difference test
- Filter leakage test
- Air flow visualization test
- Air flow direction test
- Temperature test
- Humidity test
- Recovery test
- Chamber leak test
Once a cleanroom is certified in a particular class, it is continually monitored to ensure that all parameters remain stable and the environment remains controlled.
The fifth phase: Monitoring and Control
After cleanroom certification, it is essential to implement a specialized monitoring program. We recommend utilizing statistical analysis to monitor cleanroom parameters, with Statistical Process Control (SPC) being one the key tools in this approach.
To determine the most suitable quality assurance tests for your cleanroom, consider the following critical factors:
- ISO standard requirements and GMP guidelines
- Accreditation and certification necessities, encompassing both annual and interim testing
- User Requirement Specifications (URS), risk assessment, and the monitoring plan for the manufactured product
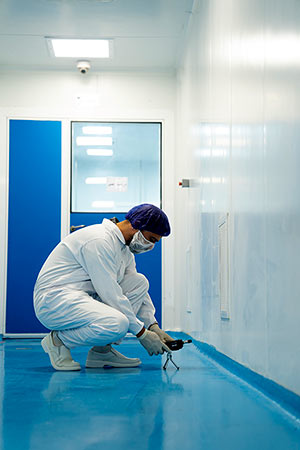